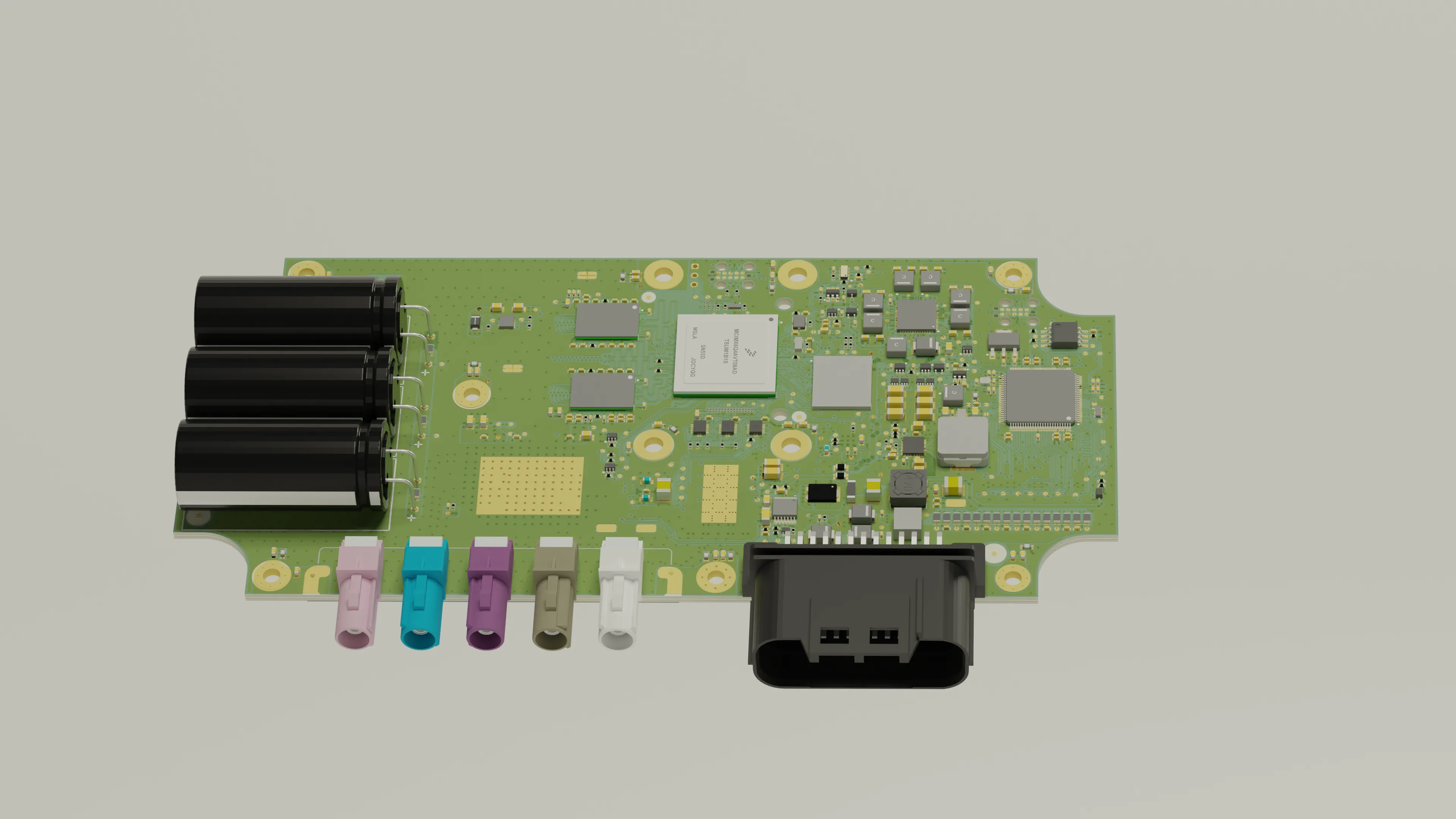
Overview
The Communication ECU is the central component of vehicle connectivity. It ensures secure data exchange, enabling features such as telemetry, fleet management, vehicle health monitoring, and over-the-air software updates.
Features highlight
- LTE Cat.4 mobile connectivity with eSIM (eUICC) and optional NanoSIM (4FF) slot or Sim-Chip (MFF2) module.
- WiFi 6
- BLE 5.3
- GNSS: GPS, BeiDou, GLONASS and Galileo navigation
- 8x CAN-FD 5 Mbit/s ports
- 100BASE-T1 100 Mbit/s Automotive Ethernet port
- Fully operation in -40 … +70 °C ambient temperatures
- IP5K3 protection rating
- SAL4 (highest cyber Security Assurance Level)
- ASIL-QM (Quality-Managed Automotive Safety Integrity Level)
- Backup supercapacitor power source for a clean shutdown in case of vehicle power failure.
- Low power consumption features:
- Multiple power domains for selective activation in low-power states
- CAN/CAN-FD partitioned networking allowing wake-up only upon receiving a specific CAN message (i.e., directly addressed)
- Wireless wake-up support for WiFi, Bluetooth and LTE
- RTC timer wake-up
My Contribution to the Project
As part of this project, my responsibilities included:
- Requirements engineering using Siemens Polarion
- Managing project in the Siemens Teamcenter
- Leading a team of two hardware engineers and a mechanical engineer
- Aligning the project with Functional Safety and Cyber Security teams
- Developing the high-level architecture
- Developing the Hardware-Software Interface (HSI)
- Ensuring compliance with ISO 26262 and achieving the ASIL-QM target
- Leading DFMEA analysis group
- Performing Simulations (GNU Octave, Python, PDN Analyzer, Signal Integrity)
- Final PCB Design in Altium Nexus (an Altium Designer-based PLM)
- Design for Manufacturing (DFM) and industrialization
- Developing validation and verification workflows
- Writing Python scripts for breadboard prototypes
Project Challenges
This project began as an effort to industrialize a proof of concept, fix known issues, and address new stakeholder requirements. One of these requirements was the need for a backup power source to retain the last CAN and Ethernet communication frames and ensure a clean shutdown in case of an EV low-voltage power failure.
While this seemed straightforward on paper, achieving the required 15-second shutdown interval posed significant challenges. Extensive simulations were necessary to guarantee this behavior under all specified environmental conditions and throughout the vehicle’s lifetime.
Another major challenge originated from the device’s operating environment requirements. It had to function within a space-constrained vehicle compartment with limited airflow, imposing strict thermal management requirements. Working closely with the mechanical engineer, we conducted multiple layout-simulation iterations to develop a solution that kept heat-sensitive components within safe operating temperatures, ensuring the device’s longevity and reliability.